Strongback Reinforcement System
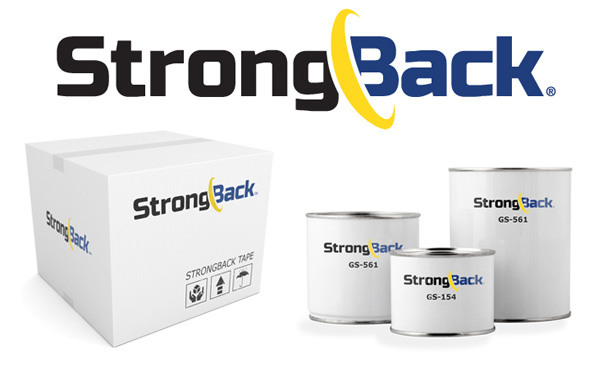
Solutions by Industry
Energy
StrongBack is in use world-wide throughout the oil and gas industry in exploration, drilling, transportation, and refining activities. It is the chosen pipeline repair and remediation solution by experienced petrochemical engineers for it’s strength, versatility and simplicity of application.
In an industry where continuity of service is critical, StrongBack provides for a fast and safe repair with no need to remove the pipe from service. No hot work is required, and no special tools or extensive training is required. Because StrongBack is non-regulated, it can be rapidly shipped by commercial passenger service to any point in the world.
StrongBack’s water activation and wet-layup application means that it is at home in the water. Underwater installation by divers can usually be achieved without the need and expense of a dry habitat. No underwater welding is required to return a compromised underwater pipeline to full-strength.
StrongBack is ideally suited to adverse environmental conditions and applications where less-than-perfect surface preparation is possible. When proper installation procedures are followed, mud, water, snow and ice will not interfere with StrongBack’s effectiveness or compromise the integrity of the repair. StrongBack is in use today in climates ranging from permafrost to equatorial jungles and deserts.
Structural
StrongBack’s great strength, load transfer capabilities, ability to conform to irregular shapes, and long lifespan make it an excellent solution for structural reinforcement applications. StrongBack can be used to encapsulate, seal and protect other repairs.
StrongBack adheres strongly to steel, copper, PVC, gel coat, galvanizing and most other engineering materials. As a reinforcement solution, it can be used to wrap concrete footings and pilings, above, below, and at the water line.
StrongBack is ideally suited to adverse environmental conditions and applications where less-than-perfect surface preparation is possible. When proper installation procedures are followed, mud, water, snow and ice will not interfere with StrongBack’s effectiveness or compromise the integrity of the repair. StrongBack is in use today in climates ranging from permafrost to equatorial jungles and deserts.
Marine
There is no more adverse or corrosive environment than the sea and due to its simple wet-layup application and water-activated resin component, StrongBack is at home in the water.
StrongBack can be applied in the splash zone and underwater, generally without the need and expense of a dry environment or habitat. No underwater welding is required to return a compromised underwater pipeline to full-strength. The StrongBack application procedure is simple and fast, limiting the amount of time that a diver or technician must spend in adverse conditions.
For repairs in the splash zone, where less-than-perfect surface preparation is possible, water will not interfere with StrongBack’s effectiveness or compromise the integrity of the repair.
Due to its great strength, StrongBack is ideally suited for abrasion prevention applications, where persistent abrasion by flotsam, jetsam and marine debris can deteriorate platform risers, pipes, footings and pilings.
StrongBack is widely used by the marine sector in oil and gas exploration and recovery, shipping, port operations and bridge maintenance.
Solutions by Application
Pipe Repair
The StrongBack composite reinforcement system provides for fast, economical, strong, and long lasting repair of damaged or degraded pipe and can serve as a permanent, high strength alternative to metal Sleeves, welding and other mechanical repairs.
StrongBack GS-154 Epoxy, when used in conjunction with the StrongBack tape and GS-561 Epoxy system, is capable of filling critical voids and cracks quickly. Pipe can often be fully restored to its original state of integrity, and at a very low-cost when compared to other repair methods, replacement of the pipe, or the loss of revenue resulting from an interruption in service.
StrongBack’s wet-layup application and water-activated resin allows pipe to be repaired without the need for welding or hot work. This drastically reduces the risk of mishap and allows the pipe to remain in service, with no interruption to normal operations.
StrongBack can be a permanent, high strength alternative to metal Sleeves, welding and other mechanical repairs. Installation can be completed in minutes and without requiring any special tools. A high post-cure strength is achieved by the material’s inherent strength, physical characteristics and a complete fit-up integrity and conformity between the reinforcing wrap and the pipe.
Pipe Reinforcement
Compromised, corroding, and deteriorating pipelines represent one of the greatest challenges to the safe, cost-effective, and efficient operation of drilling, transfer, storage, and refinement activities in the oil, nature gas and petrochemical sectors. Public utilities such as water works and natural gas face similar challenges.
StrongBack composite reinforcement products provide for fast, economical, strong, and long lasting reinforcement of degraded pipe. StrongBack’s wet-layup application and water-activated resin allows pipe to be reinforced without the need for welding or hot work. This drastically reduces the risk of mishap and allows the pipe to remain in service, with no interruption to normal operations.
StrongBack can be a permanent, high strength alternative to metal Sleeves, welding and other mechanical repairs. Installation can be completed in minutes and without requiring any special tools. A high post-cure strength is achieved by the material’s inherent strength, physical characteristics and a complete fit-up integrity and conformity between the reinforcing wrap and the pipe.
The StrongBack Composite Systems consists of just two (2) components, the GS epoxy load transfer/coating agent and the StrongBack Tape. The epoxy coating is applied over the damaged or corroded pipe surface. StrongBack tape is then wrapped over the epoxy, either circumferentially over itself or in a helical pattern if the repair length is extensive, curved or oddly shaped, to the predetermined number of plies. This combination of products transfers the hoop stresses from the damaged pipeline to the composite StrongBack sleeve.
StrongBack is ideally suited to adverse environmental conditions and applications where less-than-perfect surface preparation is possible. When proper installation procedures are followed, mud, water, snow and ice will not interfere with StrongBack’s effectiveness or compromise the integrity of the repair. StrongBack is in use today in climates ranging from permafrost to equatorial jungles and deserts.
Dielectric Insulation
Pressure-, heat- and wind-generated static electricity, as well as electricity from improperly insulated conductors, poses a threat to efficient and safe operations across a wide range of activities and industries. The high dielectric strength of the StrongBack Composite System is ideally suited to dielectric insulation applications. It is non-conductive up to 16,000 volts in its cured state and can be used to cover and insulate electrical connections and apparatus. StrongBack is currently being used as a dielectric insulator by nuclear and electric power plants, petroleum exploration and drilling activities, steel mills and manufacturing facilities.
Abrasion Prevention
StrongBack’s strength and long lifespan make it well-suited for use as a cost-effective abrasion prevention measure.
Abrasion poses a risk to pipelines and structures above ground, below ground and at sea. Above ground abrasion risks include wind borne abrasives, vegetation and even animal life. Below ground, pipe is subjected to thermal expansion and contraction, bringing it into abrasive contact with rock, roots and soil. At sea, continual abrasion by flotsam, jetsam and marine debris can deteriorate platform risers, pipes, footings and pilings.
StrongBack is ideally suited to adverse environmental conditions and applications where less-than-perfect surface preparation is possible. When proper installation procedures are followed, mud, water, snow and ice will not interfere with StrongBack’s effectiveness or compromise the integrity of the repair. StrongBack is in use today in climates ranging from permafrost to equatorial jungles and deserts.
Corrosion Prevention
Corrosion poses a risk to pipelines and structures above ground, below ground and at sea. At sea, continual wave action and air-water interchange will quickly corrode platform risers, pipes, and all other metal structures.
StrongBack is a highly-effective anti-corrosion protection solution due to its simple wet-layup application and water-activated resin component. StrongBack is at home in the water, buried below ground, and in the wet environments where corrosion poses its greatest challenges.
StrongBack can be a permanent, high strength alternative to highly corrosive metal sleeves, welding and other mechanical repairs and provides for a complete fit-up integrity and conformity between the reinforcing wrap and the pipe. When metal- or welding-based repairs are required, StrongBack can be used to encapsulate and seal these.
StrongBack can be applied in the splash zone and underwater, generally without the need and expense of a dry environment or habitat. No underwater welding is required to return a compromised underwater pipeline to full-strength. The StrongBack application procedure is simple and fast, limiting the amount of time that a diver or technician must spend in adverse conditions.
Structural Repair and Reinforcement
StrongBack is one of the most trusted, proven and economical methods of structural repair and reinforcement. Choosing StrongBack can often negate the need for re-pouring structural concrete, replacing iron work, or complicated grafting and welding approaches. StrongBack is widely used in the repair and lifespan extension of bridges, towers, pilings, piers, and offshore platforms.
StrongBack adheres strongly to steel, copper, PVC, gel coat, galvanizing and most other engineering materials. As a reinforcement solution, it can be used to wrap concrete footings and pilings, above, below, and at the water line.
StrongBack’s great strength, load transfer capabilities, ability to conform to irregular shapes, and long lifespan make it an excellent solution for structural reinforcement applications. StrongBack can be used to encapsulate, seal and protect other repairs.
While StrongBack’s water activation and wet-layup application means that it is at home in the water, it is not limited to use in the marine, energy and infrastructure sectors. StrongBack, as a repair and reinforcement solution, is a long-term and cost-effective solution wherever structural metal or concrete is in use.
StrongBack is ideally suited to adverse environmental conditions and applications where less-than-perfect surface preparation is possible. When proper installation procedures are followed, mud, water, snow and ice will not interfere with StrongBack’s effectiveness or compromise the integrity of the repair. StrongBack is in use today in climates ranging from permafrost to equatorial jungles and deserts.
Typical StrongBack Repair
Product Data Sheets
StrongBack Tape
StrongBack GS-561 Epoxy
StrongBack GS-154 Epoxy
StrongBack Application Video
StrongBack application is fast, simple, and forgiving, with no special tools or training required.
View the video below. For a higher resolution version, click here to watch the video in a new window or tab.
Rapid Worldwide Delivery
StrongBack ships non-regulated by passenger or cargo air to any point on the globe.
StrongBack Users Worldwide
StrongBack is in use worldwide throughout the energy, utility, structural, and marine sectors. It is the chosen pipeline repair and remediation solution by experienced remediation engineers for it's strength, versatility and simplicity of application.
- AGIP (Nigeria) Oil Co
- Amoco Canada
- Arabian Oil Company
- BP West Java
- British Gas Corporation
- British Petroleum
- Brunei Shell Petroleum
- Burren Petroleum
- Cabinda Gulf Oil Co.
- Chevron Nigeria
- Chevron Pipeline Co
- Chinese Petroleum Corporation
- Citgo / Lyondell
- Conoco Inc
- Enbridge Pipelines
- ENI Iraq
- Enron Corporation
- Exxon Chemical Co
- GUPCO, Egypt
- Husky Oil, Canada
- Interprovincial Pipeline
- Kinder Morgan Energy
- Kuomi Arctic Oil
- Lakehead Pipeline
- Marathon Oil
- Maxus Energy
- Mobil Oil Corporation
- Nigerian National Oil Corp
- Nippon Oil Malaysia
- Petronas Carigali
- Petroleos Mexicanos
- Petroleo Brasiliero SA
- Petroleum Development of Oman
- Philippine National Oil Corp
- Saudi Aramco
- Sarawak Shell Co
- Shell Nigeria
- TengizChevroil
- TotalFinaElf Indonesia
- Unocal
- VICO / Pt. Badak